The US wholesale trade industry generates around $670 billion every month—a market too big for sellers to ignore. While more businesses are entering wholesale ecommerce, finding and partnering with trustworthy suppliers and sourcing products can feel overwhelming.
This guide will help you understand how wholesale buying works, explore your sourcing options, and learn how to find wholesale or dropshipping suppliers that match your business needs.
Whether you’re just starting out or looking to expand your product line, you’ll discover practical strategies to build reliable supply partnerships.
What is a wholesale supplier?
A wholesale supplier buys products directly from the manufacturers and sells them to retailers. The wholesale model gained popularity during the rise of mass production in the 19th century.
Wholesalers serve as intermediaries in the supply chain, buying products from manufacturers or distributors in large quantities at discount rates. They pass these savings on to retailers, who typically pay between 60% and 70% of the final consumer price. Most wholesale suppliers have product licenses and offer special pricing that’s only available to retail partners.
How to find reputable wholesale suppliers
Finding the right suppliers for your business takes time and research. Here’s what to look for:
Product quality
Do some market research before placing big orders. Some marketplaces have more knockoffs and low-quality items than others. Get samples to check quality yourself—this helps you avoid getting stuck with products you can’t sell.
Pricing and negotiation
Keep track of wholesale prices and don’t be afraid to negotiate. Most suppliers offer better deals when you buy more. A 10% discount is pretty standard and shows you’re getting fair rates.
Customer service
Choose suppliers who have a track record of solving problems quickly. This is especially important if you’re dropshipping. Check reviews and ask how they handle issues like damaged items or shipping delays.
Shipping speed
Most customers view fast delivery as taking less than three business days, so ask suppliers about how long orders take to process, which shipping carriers they use, typical delivery times, and if they offer options for rush orders.
7 leading wholesale suppliers
Want to offer a variety of products or compete on price? Here are some great wholesale marketplaces to check out:
1. Shopify Collective

Shopify Collective lets you buy and sell wholesale products from your online store, retail locations, and social media accounts.
This platform is perfect if you:
- Don’t have much storage space but want to sell more products
- Want to keep cash flow healthy (you only pay suppliers after making a sale)
- Dream of creating an online department store with multiple brands
Take luxury fashion brand Larroude, for example. It uses Shopify Collective for “Colléct”—its curated marketplace of emerging brands. “Through a seamless expansion into other luxury brands, Collective drove an impressive 21% month-over-month revenue increase, showcasing the power of brand collaborations and the ability to tap into new categories,” says Bianca Inocencio, business solution specialist at Larroude.
2. Alibaba and AliExpress
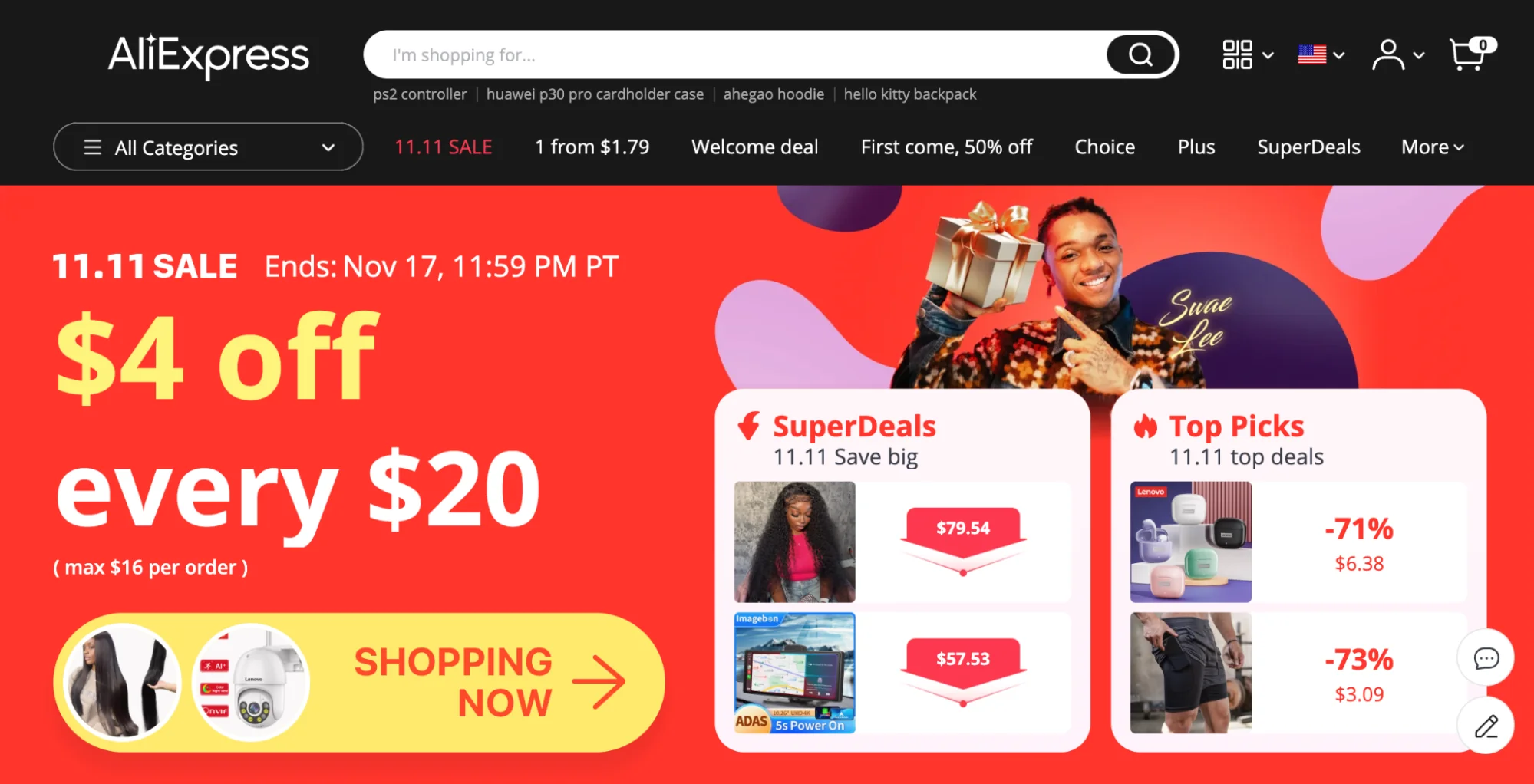
Alibaba and it's partner site, AliExpress, are common destinations for global retailers looking to source products from Chinese wholesalers.
Just starting out? Try AliExpress first purchase a single product before jumping into Alibaba’s world of wholesale bulk buying. These platforms are great for:
- Finding affordable goods from China
- Exploring tons of products at different price points
- Creating your own private label products
Shipping from China has gotten much better thanks to ePacket delivery. Back in 2011, the US Postal Service started offering First Class service and delivery tracking for ePackets. This means getting products from Chinese suppliers is now faster and cheaper than ever.
3. DHgate

DHgate is another Chinese wholesale platform with competitive prices. Just keep in mind that it’s known for replica goods. If you need authentic products, you’ll want to look carefully at who you’re buying from.
What makes DHgate worth checking out:
- Great prices across different products
- Lots of options for any type of store
- Easy-to-use rating system to check supplier reliability
4. EK Wholesale

EK Wholesale has been in the game for more than 30 years, making it a go-to supplier in Europe. Based in Scotland, it focuses on quality wholesale clothing and ships free to the UK mainland when you spend more than £250.
EK Wholesale might be right for you if you:
- Run a fashion store
- Want to start your own clothing brand
- Sell mostly to European customers
5. Faire

Faire is popular with North American merchants. You’ll find lots of suppliers from across the continent selling everything from beauty products to office supplies to pet accessories.
Faire is also great for dropshippers. Many of its suppliers offer free shipping, which helps keep your costs down when you’re just starting out.
Faire offers two ways to use their platform with Shopify:
- Buy wholesale products through the Faire: Buy Wholesale app
- Sell products to retailers globally with the Faire: Sell Wholesale app
6. Wholesale Central

Wholesale Central keeps things simple. Its no-frills website connects you with more than 1,400 suppliers offering more than 700,000 products—and there’s no membership fee.
What makes Wholesale Central stand out:
- True wholesale pricing (you’ll need your business ID and tax number )
- Easy search tools to find dropshippers in your area
- No registration needed—start connecting with suppliers right away
7. IndiaMart

IndiaMart shines in specific industries. Consider this marketplace if you’re selling:
- Medical supplies
- Chemical products
- Industrial equipment
- Automotive parts
- Over-the-counter pharmaceuticals
It’s one of the few wholesale platforms that work with these specialized industries, making it valuable for niche sellers.
Other considerations for finding suitable wholesale suppliers
Finding the right supplier takes some digging. Here are some common pitfalls to watch out for:
Location matters
Fast delivery is a must for today's shoppers. Think about where your customers are. If you're selling to European customers, shipping from a German supplier will be faster and cheaper than shipping from China. Also consider navigating tariffs and customs requirements when sourcing internationally, as these can significantly impact your costs and delivery times.
Budget wisely
Find the sweet spot with your spending:
- Order enough to get wholesale benefits
- Don’t overcommit to untested products
- Set clear budget limits
- Calculate costs before ordering
Watch for hidden costs
Most wholesale suppliers charge membership fees—that’s normal. But make sure you understand all the costs upfront. Ask about:
- Membership fees
- Minimum order requirements
- Shipping costs
- Payment terms
Check legitimacy
Be wary of wholesale suppliers that sell to the public. Real wholesale suppliers need to see your business ID—it’s how they protect their wholesale pricing.
How wholesale suppliers help your business
Wholesale suppliers let you focus on what matters: picking great products (so you don’t have to develop your own products), marketing them well, and providing excellent customer service. Working with wholesalers gives you several advantages:
- Buy what as you need without expensive storage costs
- Quickly restock popular items through established supplier relationships
- Get better prices that lead to healthy profit margins
- Skip the product development process—saving money and time
Understanding dropshipping suppliers
Dropshipping is a different fulfillment method from traditional wholesale. Instead of keeping inventory, you purchase products from third-party suppliers who ship directly to your customers. Think of it as combining wholesale purchasing with third-party fulfillment.
The dropshipping business model helps you avoid:
- Managing inventory
- Packing orders
- Handling shipping
Just starting out? Consider using a dropshipping app that connects with your online store. If you’re more experienced or have a specific niche, you might prefer working directly with wholesale suppliers for better pricing.
Learn more: 150+ Dropshipping Products to Sell for Profit
Unconventional ways to find wholesale suppliers
While wholesale marketplaces are the easiest ways to find suppliers, thinking outside the box might lead you to better deals. Here are some creative approaches:
- Visit industry trade shows to meet suppliers in person
- Join social media groups in your niche to connect with other merchants
- Become a member of trade organizations in your product category
Meeting suppliers face to ace can be especially valuable. These personal connections often lead to stronger relationships, better prices, and more flexible terms for bulk purchases.
Questions to ask potential suppliers
Before reaching out to suppliers, gather your business license and tax documents—many won’t even discuss pricing without them. This is normal: certified wholesalers can only sell to businesses, not consumers.
When you do call, here are key questions to ask:
Minimum orders and pricing
- What are your minimum order quantities (MOQs)?If you’re looking to order 100 pieces of jewelry but the supplier only offers discounts on orders of 500 pieces or more, then that’s an issue.
- What’s the cost per unit?
- Do you offer volume discounts?
Don’t order more than you need just to get a better price. An unsold product that seemed like a bargain can quickly become a costly mistake.
Policies and timing
- What’s your return policy? Who covers shipping for returns?
- How long does it typically take to fulfill orders?
- How do you handle out-of-stock situations?
Clear shipping times help you set customer expectations. Long delays or unclear restocking timelines can lead to unhappy customers.
Remember: Most terms are negotiable, especially once you build a relationship with your supplier.
Learn more: The Ultimate Wholesale Terminology Glossary
Final checks before partnering
Before signing any agreements, take these important last steps:
Ask for references. Request contact information for current customers. Be cautious if a supplier hesitates to share references—this could be a red flag.
Check insurance. Make sure they have product liability insurance. This protects you if customers are injured by faulty products. A supplier without insurance puts your business at risk.
Review the numbers. Start small with new suppliers, even if bigger discounts are tempting. Calculate all your costs upfront, including shipping or handling fees. Remember that unsold inventory ties up money you could use elsewhere in your business, so don’t let exciting deals push you to overextend your budget.
How to build strong relationships with suppliers
Strong supplier relationships can make or break your business. Here’s how to create partnerships that last and help both sides succeed:
Communicate clearly
Wholesale suppliers work with many brands at once, so respect their time with direct communication. Instead of vague inquiries like “I’m thinking about starting a dropshipping business,” ask specific questions like, “What’s your best price for 250 units per month?”
Think beyond your needs
Don’t just reach out when you want something. Find ways to make the relationship work for both sides. For example, ask for their preferred order form template or get the right email for accounts payable. Small things that streamline their processes can make a big difference in how they work with you.
Pay on time
Most suppliers give you a month after delivery to pay for orders, letting you sell some inventory first. Meeting these payment schedules is crucial—suppliers are running a business too. Late payment might lead to stricter terms or even losing the supplier altogether.
Give and receive feedback
It’s rare to get the working relationship right the first time. Both you and your wholesale supplier are learning about each other. Stay open to feedback—it helps solve issues quickly and builds rapport.
Show appreciation
When you find a reliable wholesale supplier, let them know. A strong relationship helps secure steady inventory and reduces stockouts. Suppliers who feel valued are more likely to prioritize your orders and offer you new items first, helping keep your product assortment fresh.
Popular wholesale products
When choosing suppliers, consider your specific product needs. While many suppliers offer general merchandise, some excel in particular niches.
Here’s what to look for in popular product categories:
Wholesale jewelry
Before placing a large order for your jewelry business, check these key details. If a supplier doesn’t provide this information, keep looking:
- Product reviews and quality ratings—do products meet customer expectations?
- Current client list—well-known retailers build confidence in the supplier
- Shipping insurance and damage policies—jewelry is small and delicate, so clarify who covers losses before ordering
Learn more: How To Get Started Dropshipping Jewelry
Wholesale clothing
Fashion is popular with dropshippers and constantly evolves with trends. When evaluating fashion wholesalers, focus on:
- Clear niche focus (women’s, children’s, or men’s wholesale clothing)
- Brand customization options, like custom t-shirts or hoodies
- Professional packaging—it’s the only channel that reaches 100% of your customers
Learn more: What Is Print on Demand and How To Start a Business
Wholesale tea and coffee
Selling coffee online offers an easy entry point into ecommerce, but has unique considerations:
- Product packaging quality is crucial since customers don’t see a logo while drinking
- Brand identity support—good suppliers in the food industry should help you build your brand
Learn more: How To Start Dropshipping Coffee
Find your perfect wholesale supplier today
Starting an online store might feel overwhelming if you don’t have products to sell. But finding reliable wholesale suppliers is easier than ever. Look for well-reviewed suppliers who know your niche, order samples, negotiate prices, and get started. Shopify is there with you at every step.
From first-time sellers to global retailers, Shopify works for everyone. See plans and pricing.
Read more
- The Ultimate Guide To Dropshipping (2024)
- How To Sell Sex Toys Online in 2024
- How To Source Products To Sell Online
- The 13 Best Dropshipping Suppliers in 2024
- How to Start a Dropshipping Business- A Complete Playbook for 2024
- How to Start an Online Boutique- A Complete Playbook
- How To Sell Wholesale: Best Products and Marketplaces (2024)
- Free Business Plan Template- A Practical Framework for Creating Your Business Plan
- 12 Checkout Process Optimization Tips to Increase Ecommerce Revenue
- Ecommerce Laws- Legal Requirements for Ecommerce Websites
Wholesale suppliers FAQ
How do I find a reliable wholesaler?
- Attend trade shows
- Use wholesale directories like Alibaba or ThomasNet
- Contact manufacturers directly
- Search online marketplaces
- Join wholesale forums
- Ask for referrals
Where can I buy bulk items to resell?
Popular wholesale websites include AliExpress, DHgate, Alibaba, and Amazon. The best choice depends on your product type.
How do I buy wholesale for a small business?
Most wholesale suppliers only sell to businesses, not to consumers. You’ll likely need:
- A business bank account
- An employer identification number (EIN)
Can I use wholesale suppliers for dropshipping?
Yes, many wholesale suppliers offer dropshipping. They’ll pick, pack, and ship orders directly to your customers from their warehouse.